A Song of Knives and Wire
By Vivienne Brooke
Blog ·
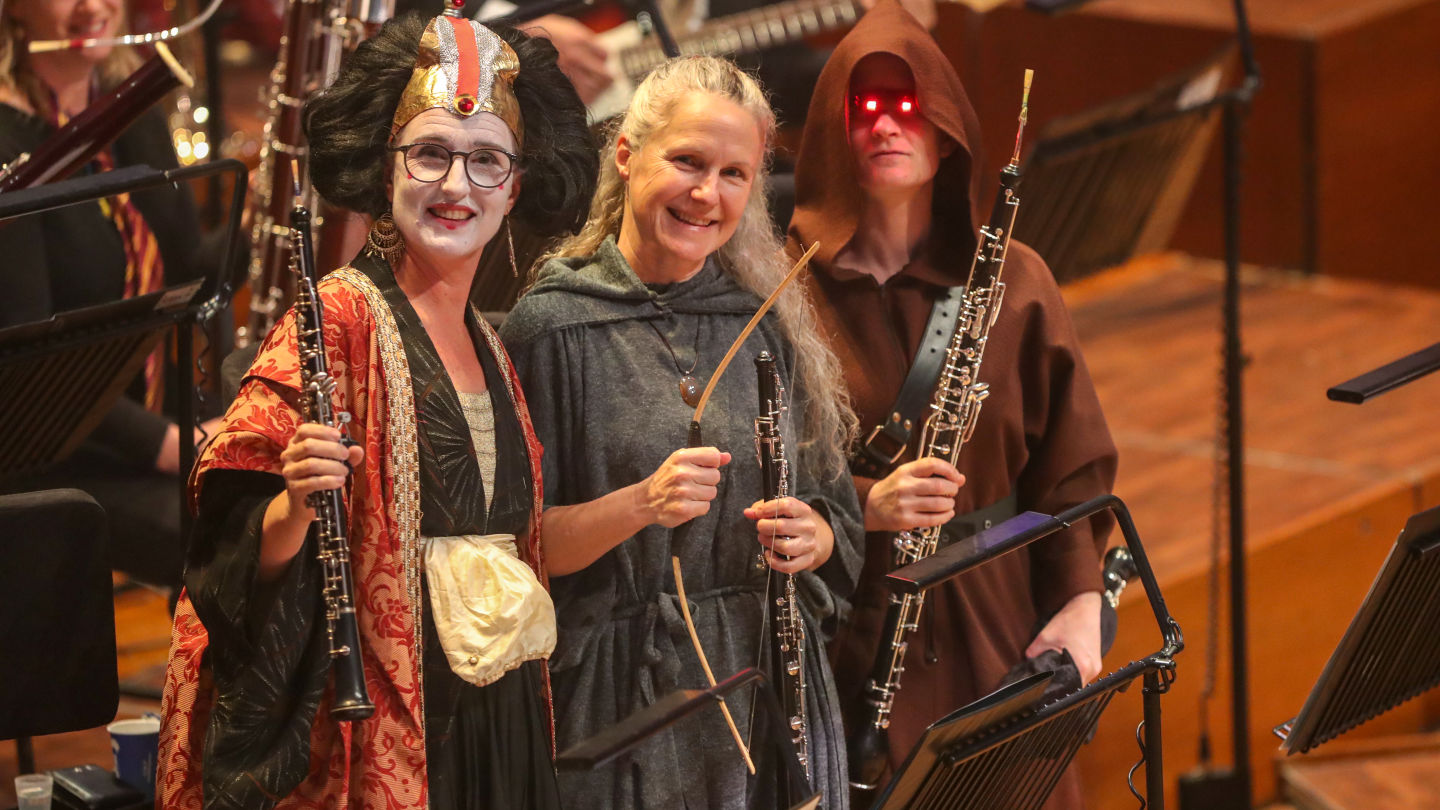
Principal Cor Anglais Vivienne Brooke (far right) with Associate Principal Oboe Sarah Meagher and oboist Alexa Murray at our 2019 CINEMATIC movie music event
Our Principal Cor Anglais takes us behind the scenes in the secret art of reed making.
Like all of my colleagues, I am trying to find things to do at home while we wait impatiently for the halls to open and concerts to resume. While many musicians enjoy relaxing with crafts such as knitting and needlework, being a double reed player comes with its own bonus crafty hobby - making our own reeds! I thought some people might be interested in a look at the weird and wonderful machines and tools that are involved in what is essentially making our own mouthpieces.
The number one question I’m asked is ‘How long does a reed last?’ to which I always hilariously answer, ‘forever, if you don't play on it.’ But seriously, unless we accidentally bash it on our teeth (you'd be surprised), they can last from a couple of weeks to a few months. The cane is a natural product that can crack or just slowly deteriorate. It also behaves differently in different temperatures or weather conditions, which is an extra bit of fun for us when performing.
‘Why do we need so many?’ Alas, because we are searching for the perfect one...! Some reeds end up having different qualities – one might be good for playing softly (but not loudly), or for lovely low notes in a second oboe part. It's like having a cutlery set except you made them all yourself! Some days you end up with a knife that would be great for carving a roast but tonight's menu is potato foam and an delicate dessert (hands up who else is keeping sane with MasterChef?).
Sometimes other musicians express envy and say, ‘wouldn't it be wonderful to be able to make your own and have the ability to control every aspect!’ To which we say a resounding ‘no’! Reeds are fiddly, time consuming, and can be quite messy…
And finally, ‘Can't you just buy them?’ to which the answer is yes, and many do, although they cost around $30 each and I'm guessing in this post-COVID world they won't be accepting returns. It's also possible to purchase cane and reeds in varying stages of completion - although here I will show the machines used to make a perfect Cor Anglais reed at home out of a stack of cane foraged from your very own home garden!*
*Not really. Like almost everything we use, it comes from a secret factory in France.
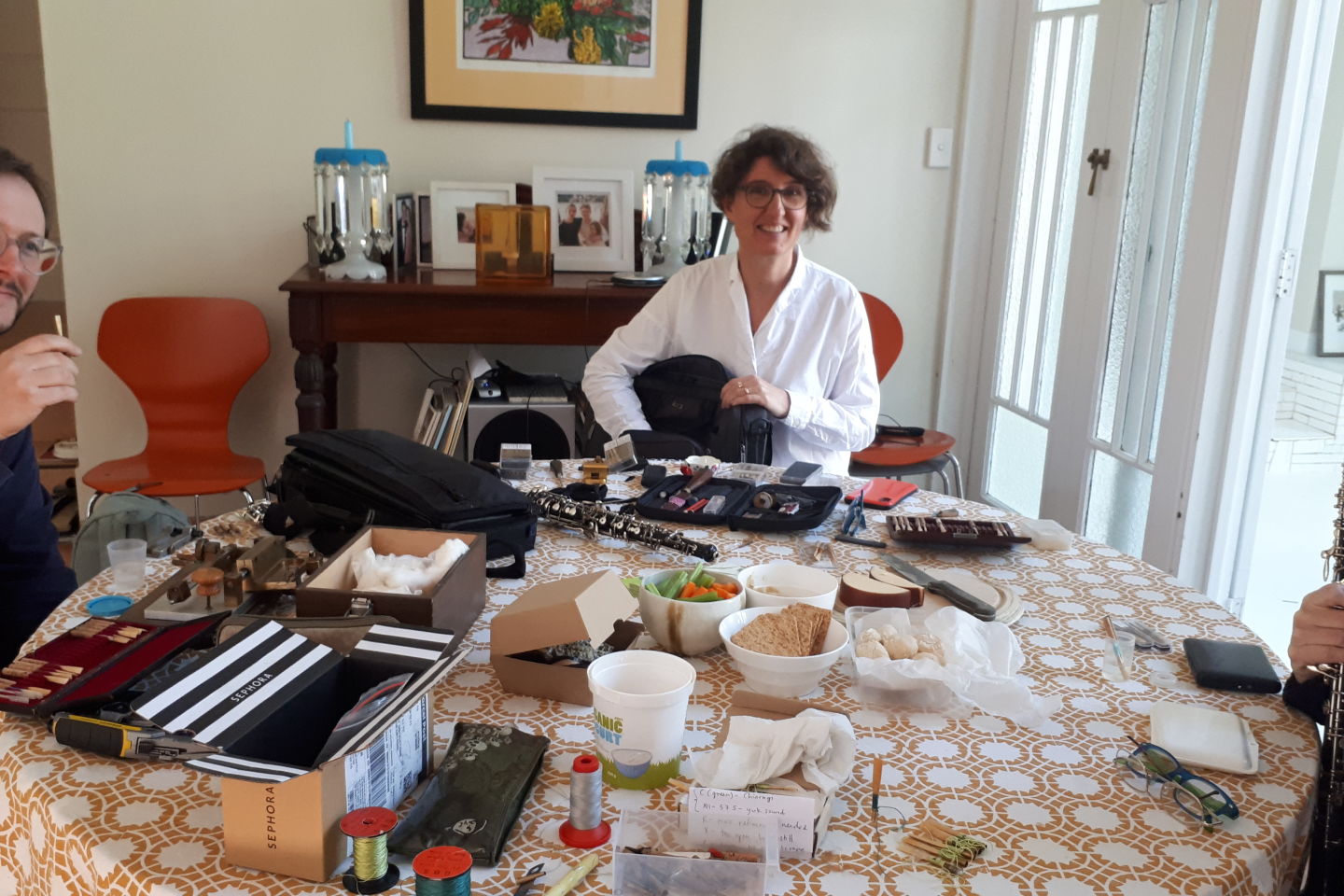
The gouger scrapes the inside of a rough semicircle of cane into a lovely smooth semicircle of cane. This machine also has a guillotine to cut the cane to the right length.
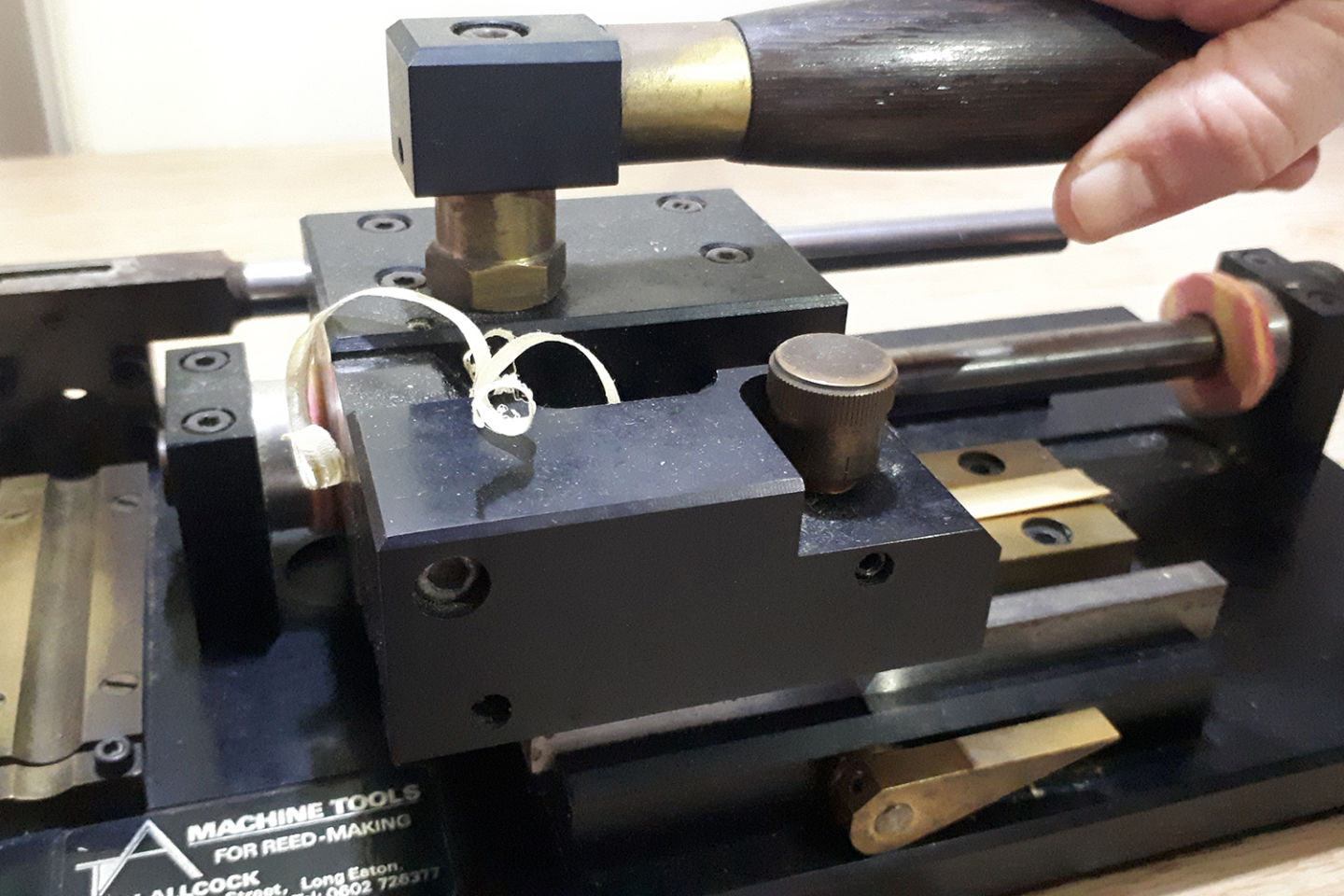
The gouger
The shaper uses blades to cut the cane on a metal template to form the tapered shape. And yes, there are hundreds of different template shapes to choose from. Feel like trying another? Simply send €86 off to France and see if you can tell the difference!
Next, the shaped cane is bound to a metal staple with thread to millimetre-precise measurements. This part, alas, does not have a machine to help with. One end of the thread is tied to something solid and pulled taut for the binding process. If you’ve ever visited a conservatorium or an oboist's house and found a table leg festooned with straggly bits of nylon thread that is the answer to your question. Oboe reeds use a metal tube with cork. I can't speak for bassoonists who do things with fire, wonderfully ornate knots and something called a reamer.
The shaper
Finally a profiler can be used to shave the tip of the reed until the reed ‘works’. This is a great time-saver but a knife is still used to finish things off.
Other tools we use include knives. For scraping the cane, and also cutting the tip (I forgot to say that after binding, the 'double' reed is still one piece of folded-over cane.) Plaques are then inserted to protect the fragile cane while scraping. Other tools include an easel - a beautiful cylindrical piece of ebony whose sole purpose is to mark the middle of a piece of cane for folding; mandrels - handles to pop the reed on while binding and scraping; cutting blocks; guillotines; as well as Stanley knives; sandpaper; pliers; wire; sharpening stones; and whatever else we can find in the shed!
The profiler
Last but not least I like to use the cut-off end of a roll of gladwrap, an essential item for wrapping the reed after it is finished and you discover air is leaking out the sides. Some oboists use goldbeater's skin, which I just googled and found is definitely not vegan. Sometimes I wonder, if the world goes plastic-free, how many rolls of gladwrap I would have to hoard...
So, there you are – a brief tour into the complex world of reed-making, and a small insight into the depths of anguish a double reed player is expressing when they say, ‘I don't have anything to play on...’
The set-up